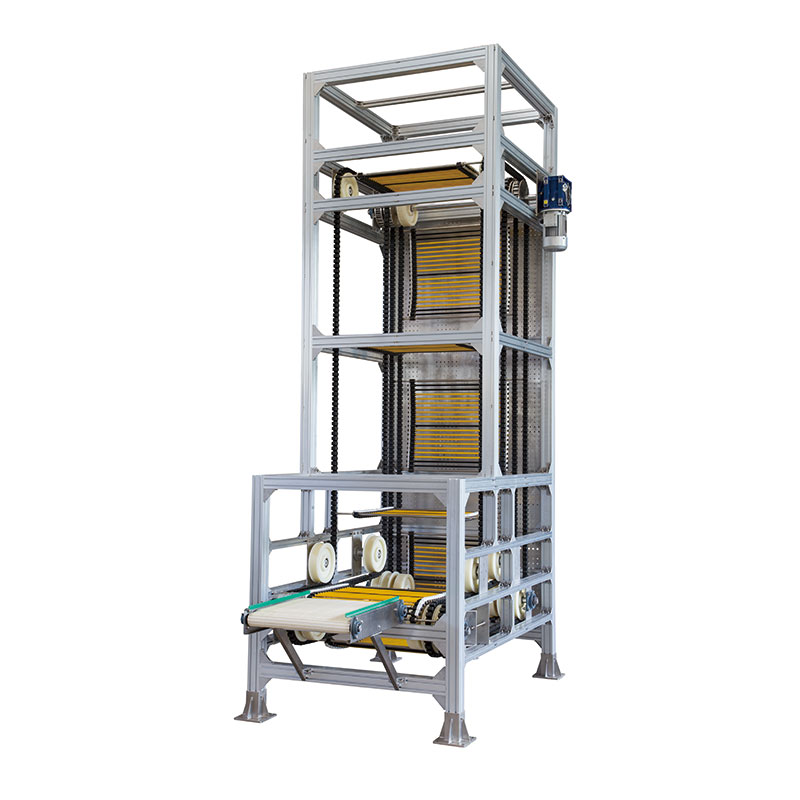
Vertical Conveying Food Continuous Elevator
Vertical Continuous Elevator
-
+86-13427473518 WhatsApp
-
kc001@jm-kc.com Email
Food Continuous Elevator is a vertical conveying equipment designed specifically for the food industry, aimed at achieving efficient, hygienic, and continuous transportation of materials. As a modern food processing auxiliary equipment, it can smoothly lift food raw materials or finished products from low to high, while ensuring cleanliness and safety during operation. This type of equipment is widely used in food processing plants that require a multi-layer layout and can meet the height difference requirements of the production line. This device can provide reliable and efficient solutions for baked goods, frozen food, and other applications that require vertical conveying.
Vertical Conveying Food Continuous Elevator Specifications
Product Name | Continuous Elevator | |
Model | KC-SJ-Z | KC-SJ-C |
Voltage | 380V3N | 380V3N |
Power | 1.5kW | 1.5kW |
Increased Height | 2-30m | 2-30m |
Chain Speed | 0.1-0.9m/sec | 0.1-0.9m/sec |
Production Capacity | 4-20pcs/min | 4-20pcs/min |
OEM/ODM | Accept | |
Compay Nature | China Manufacturers Suppliers Factory |
Vertical Conveying Food Continuous Elevator Advantage
1. Innovative transmission system:
One of the most notable features of the Vertical Conveying Food Continuous Elevator is its flexible polyurethane chain transmission system. Compared with traditional roller chains, this new transmission method completely changes the operation mode and performance of the equipment. The flexible polyurethane chain not only has excellent wear resistance and corrosion resistance, but also effectively reduces the noise and vibration generated during operation. More importantly, this material avoids the metal powder and oil pollution problems that traditional steel chains are prone to in long-term use, thereby greatly improving the hygienic performance of the equipment.
2. Efficient conveying capacity:
The conveying capacity of this equipment has been greatly optimized, and it can handle 4 to 20 products per minute, depending on the size and weight of the material and the needs of the production line. The chain speed can be flexibly adjusted between 0.1 and 0.9 m/s, and users can set it precisely according to actual production needs. In addition, the equipment supports continuous operation mode and can operate stably around the clock, significantly shortening the material transportation time, thereby improving overall production efficiency.
3. Highly customizable:
In order to adapt to the specific needs of different customers, Vertical Conveying Food Continuous Elevator provides highly customizable solutions. The tower height ranges from 2 meters to 30 meters, and users can choose the appropriate size according to the plant layout and process requirements. The equipment also supports two-way conveying function, which can not only convey materials from low to high, but also from high to low, further improving the flexibility and practicality of the equipment.
4. Intelligent control system:
Intelligence is another core advantage of Vertical Conveying Food Continuous Elevator. The equipment integrates a fully automatic intelligent control system and is equipped with an intuitive touch screen operation interface. Users can start, stop, set parameters, and perform fault diagnosis through simple touch operations. The touch screen interface design is simple and clear, and even first-time operators can quickly get started. The equipment also supports remote monitoring function, and users can view the operating status of the equipment in real time by connecting to the network, and find and solve problems in time.
5. Excellent hygienic performance:
Hygienic performance is one of the core indicators of food processing equipment, and the Vertical Conveying Food Continuous Elevator performs well in this regard. The equipment uses food-grade polyurethane material to make the conveyor chain belt. This material is not only smooth and easy to clean, but also does not produce any harmful substances. During operation, the equipment will not cause secondary pollution to the material, fully complying with strict food safety standards. The design of the equipment fully considers the convenience of cleaning. All parts that contact the material can be easily disassembled and cleaned to ensure that they can be restored to the best condition after each use.
6. Low noise and high stability:
Compared with traditional lifting equipment, the Vertical Conveying Food Continuous Elevator generates lower noise during operation, only about 60 decibels, which meets the environmental protection standards of modern factories. This is due to the use of flexible polyurethane chain belts and precise mechanical structure design, which makes the equipment remain stable and quiet at high speed. The equipment has extremely high operating stability, and there will be no obvious wear or loosening even in the case of long-term continuous operation.
7. Compact structural design:
In modern industrial production, space utilization is an important consideration. The compact structure design of the Vertical Conveying Food Continuous Elevator makes it an ideal choice for solving space limitation problems. The equipment occupies a small area and makes full use of the vertical space for material transportation. It is very suitable for production workshops with limited space but high production capacity requirements. Its modular design facilitates installation and disassembly, while also reducing maintenance costs.
8. Humanized design:
The humanized design of the equipment is reflected in many aspects. It supports both manual and automatic operation modes, and users can switch freely according to actual needs. The equipment has complete safety protection measures, including emergency stop button, overload protection device and anti-slip design to ensure the safety of operators and the equipment itself.
Vertical Conveying Food Continuous Elevator Application
1. Baking Industry:
In the baking industry, the Vertical Conveying Food Continuous Elevator is an important device that connects different production links. For example, in a bread production line, it can transport the mixed dough from the mixing area to the proofing room or forming machine; in a biscuit production line, it can smoothly transport semi-finished biscuit dough to the entrance of the baking oven. In addition, the equipment is also suitable for conveying finished products, such as lifting cooled cakes from the end of the production line to the packaging area. Because it uses food-grade polyurethane chain belts, it avoids the contamination problems that may be caused by traditional metal chains, so it is particularly suitable for baking workshops that require high hygiene standards. Whether it is a small bakery or a large industrial baking plant, this equipment can significantly improve material transportation efficiency and reduce the cost and risk of manual handling.
2. Frozen Food Processing:
The production environment of frozen food is usually extremely low in temperature, which puts higher requirements on conveying equipment. The Vertical Conveying Food Continuous Elevator can operate stably in this low-temperature environment without affecting its performance due to the cold. For example, on a frozen dumpling production line, it can quickly transport products from the quick-freezing tunnel exit to the packaging line, ensuring that the dumplings remain frozen throughout the process to avoid quality degradation. At the same time, the efficiency and continuity of the equipment make the handling of large quantities of frozen foods smoother, thus meeting the needs of modern frozen food companies for speed and precision.
3. Beverage and dairy industry:
The beverage and dairy industries have strict requirements on the hygienic performance of conveying equipment, as any contaminants may cause product quality problems or even recalls. The food-grade materials and easy-to-clean design of the Vertical Conveying Food Continuous Elevator make it an ideal choice in this field. For example, on a bottled beverage filling line, it can transport empty bottles from the ground to the top of the filler, and then send the filled bottles to the labeler or carton sealer. Similarly, in dairy production, the equipment can be used to transport milk bottles, yogurt cups or other container products to ensure that the entire process meets food safety standards.
4. Pharmaceutical industry:
The production process of the pharmaceutical industry is highly dependent on automation and precise control to ensure the safety and consistency of drugs. The Vertical Conveying Food Continuous Elevator excels in this regard, with its intelligent control system and hygienic design fully complying with GMP (Good Manufacturing Practice) requirements. For example, in a tablet production line, the device can transport compressed tablets from a tablet press to a coating machine or packaging machine; in powdered raw material processing, it can safely lift raw materials from a storage area to a mixing tank. In addition, the low noise and high stability of the equipment also provide an ideal solution for clean workshops, reducing the risk of contamination caused by human intervention.
5. Chemical Industry:
Although the Vertical Conveying Food Continuous Elevator was originally designed for the food industry, its excellent corrosion resistance and sealing properties also make it very suitable for the chemical industry. For example, it can be used to transport granular raw materials in fertilizer production, or to lift barreled liquids in paint manufacturing. The modular design of the equipment allows the material and structure to be adjusted according to different chemical properties to meet specific process requirements. In addition, its automated operation mode helps reduce the risk of workers being exposed to hazardous chemicals and improves production safety.
6. Logistics and warehousing:
In modern logistics centers and large warehouses, the effective use of vertical space is essential. The Vertical Conveying Food Continuous Elevator can help achieve the rapid transfer of goods between different floors. For example, in an e-commerce distribution center, it can lift packages from the sorting area to the shipping platform; in a multi-layer shelf system, it can transport pallet goods from the ground to the high-level shelves, or transport goods on the shelves back to the ground for replenishment. This efficient vertical transportation method not only saves labor costs, but also optimizes the warehouse management process and makes logistics operations smoother.
Vertical Conveying Food Continuous Elevator Maintenance
1. Regular cleaning:
To ensure the hygienic performance of the equipment, it is recommended to thoroughly clean the polyurethane chain belt and housing every day. Since this equipment is widely used in the food industry, any residue or contaminants may affect the product quality, so cleaning is essential. Use warm water and neutral detergent to clean the surface of the chain belt and the equipment housing. Avoid using strong acids, strong alkalis or other corrosive detergents to avoid damaging the polyurethane material. After cleaning, the surface of the equipment should be wiped dry with a clean soft cloth to prevent moisture retention from causing rust or breeding bacteria. Especially in food processing environments, the cleaning frequency can be adjusted according to the production cycle. For example, during high-volume production, the number of cleanings can be increased to maintain optimal hygiene.
2. Lubrication check:
Although the polyurethane chain belt itself has self-lubricating properties and does not require additional lubricants, other moving parts in the equipment (such as bearings, gears and chain tensioners) still need to be lubricated regularly. It is recommended to check the lubrication of these parts once a month and add an appropriate amount of food-grade lubricant according to the actual degree of wear. Food-grade lubricants not only reduce friction, but also avoid contamination of food. When adding lubricating oil, be careful not to add too much to prevent the oil from leaking onto the conveyor belt and affecting the product quality. At the same time, excess oil stains should be removed after lubrication to keep the equipment clean.
3. Fastener inspection:
During the operation of the equipment, due to vibration and load changes, fasteners such as bolts and nuts may gradually loosen, thus affecting the stability and safety of the equipment. Therefore, it is recommended to conduct a comprehensive inspection of the equipment every month, paying special attention to fasteners in key parts, such as chain belt fixing points, motor brackets and tower body connections. If looseness is found, it should be tightened immediately with appropriate tools. In addition, the fasteners should be regularly checked for rust or damage, and new parts should be replaced in time if necessary to ensure long-term and stable operation of the equipment.
4. Electrical system maintenance:
The electrical system is the core part of the equipment, and its normal operation is directly related to the efficiency of the entire production line. It is recommended to check the control panel, cable connectors and sensors weekly to ensure that there is no looseness, damage or aging. If cracks are found in the cable sheath or poor contact of the connector, they should be replaced or repaired in time. In addition, in humid or dusty environments, special attention should be paid to the moisture and dust protection of electrical components. Sealing covers or protective coatings can be used to extend the service life. For touch screen operation interfaces, it is recommended to clean the screen surface regularly to prevent dust or stains from affecting touch sensitivity.
5. Wear detection:
Polyurethane chains and guide rails are key components of the equipment. After long-term use, they may wear or deform, which will affect the conveying efficiency and stability. It is recommended to conduct a comprehensive inspection of the chains and guide rails every quarter to observe whether there is excessive wear, cracks or deformation. If obvious scratches or thinning of the chain surface are found, a new chain should be replaced in time. In addition, the smoothness of the guide rails also needs to be paid attention to. If there are burrs or depressions, sandpaper or special tools should be used to repair them to ensure smooth operation of the chain. Regularly recording the wear can help predict the replacement cycle of components, so as to prepare spare parts in advance.
6. Calibration and debugging:
With the increase of usage time, the operating parameters of the equipment may deviate slightly, such as the chain speed slowing down or the conveying height being inaccurate. Therefore, it is recommended to carry out comprehensive calibration and commissioning at least once a year, including the adjustment of key parameters such as chain belt speed, conveying height, tension, etc. During the calibration process, the standard values in the equipment manual should be strictly followed, and professional measuring tools (such as laser rangefinders or tachometers) should be used to ensure accuracy. In addition, software updates should be carried out on the intelligent control system to optimize equipment performance and fix potential vulnerabilities.
7. Train operators:
The professional skills of operators directly affect the use effect and maintenance quality of equipment. Therefore, enterprises should regularly organize operators to participate in equipment use and maintenance training to help them familiarize themselves with the equipment's operating specifications, daily maintenance points, and methods for handling common faults. The training content can include the basic principles of the equipment, safe operating procedures, cleaning and lubrication techniques, and how to correctly read and adjust operating parameters. Through systematic training, not only can the operator's sense of responsibility be improved, but the risk of human operating errors can also be effectively reduced, thereby extending the service life of the equipment.
Production Environment
With advanced equipment and skilled personnel, we provide customized design, manufacturing, installation, debugging, and after-sales maintenance of intelligent mechanical equipment.
Engineering Cases
We deeply understand that every customer has diverse needs. Therefore, we provide professional customized baking solution services, tailoring baking engineering machines according to customers' actual requirements. From the functional configuration to the design of the machine, we fully consider customers' personalized needs to ensure that every machine becomes a proud product for the customer.
Application Scenarios
KC-SMART provides cutting-edge solutions tailored to the baking industry. Our intelligent mechanical equipment is widely used in the production of diverse baked goods, including bread, mooncakes, cookies, and cakes.
Exhibitions
At KC-SMART, we actively participate in industry-leading trade shows to showcase our advanced intelligent mechanical equipment for the global baking industry. These exhibitions provide an excellent platform to connect with clients, discuss their specific needs, and demonstrate our solutions for powder transportation, mixing, fermentation, baking, cooling, and material handling.
KC-SMART founded in 2000, is a high-tech enterprise dedicated to providing global baking food customers with one-stop solutions, including customized design, manufacturing, installation, debugging, and after-sales maintenance of intelligent mechanical equipment. Guided by the values of "willingness to work hard and innovate, and win-win future" and the business philosophy of "honesty, quality, responsibility, and respect for talents," the company strives to deliver the best possible service.
Located at No. 3 Jinyi Road, Pengjiang District, jiangmen City, Guangdong Province, the company covers an area of over 10,000 square meters. Its product line includes intelligent mechanical equipment for powder transportation, mixing, fermentation, baking, cooling, demolding, and material handling, among others. The company also holds multiple practical invention patents.
Looking ahead, Jiangmen Kenchuang Conveying Machinery Co, Ltd. will continue to uphold the spirit of innovation, constantly improve product quality and service levels, and provide even more intelligent and efficient mechanical equipment solutions for global baking food customers. Together, we aim to create a brighter future for all.